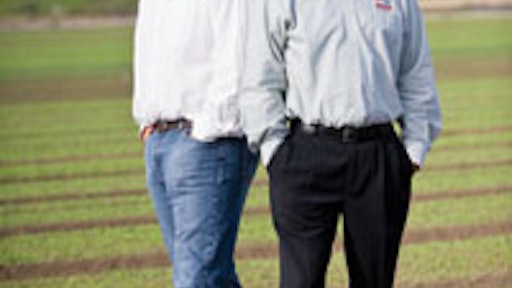
Word arrives that a product you manufacture is sickening consumers. A common lot number associated with all packages of the problematic product is discovered. How quickly can you determine where every case of that product is, to whom and when it was shipped, or where it is in your supply chain?
How long will it take to identify every other product you've processed that shares ingredients from the same lots that went into the problem product? Or every package that was processed on the same manufacturing line that same day?
Then, how long will it take for you to notify every customer who received that product and arrange for its return and/or disposition?
For some companies, the answer to these questions is mere minutes, followed by hours. For others, it's a giant question mark.
Yet the answer, in extreme cases, can have dire impacts on the health and safety of consumers and on your company's future. As a cautionary tale, witness the fate of Topps Meat Co., Newark, the now defunct, 67-year-old frozen beef patty processor forced to shutter its doors last fall after a botched response to the second largest beef recall in U.S. history.
No one wants to think the unthinkable will happen to them, but as with any form of insurance, no matter how unlikely the hazard, the key to survival and recovery lies in making the necessary preparations beforehand, just in case. No insurance company will sell you a policy the morning after the hurricane.
"In the event of a recall, you can't ever really mitigate the cost of disposing of the product, or the time involved in dealing with the situation. But by providing accurate information to the public in a very timely manner, you can maintain customer confidence that the company is doing the right thing, that you're prepared to do whatever is necessary to protect consumers. Otherwise, you could end up losing your business," comments Will Daniels, vice president of quality, food safety and organic integrity for Earthbound Farm, San Juan Bautista, CA.
The spate of recall stories in the media over the last few years has no doubt raised awareness among manufacturers and retailers of the risks.
"There is certainly much more interest in discussing what needs to be done to prepare. Companies are realizing that being ready for a recall is one way they can mitigate their risk and properly control the event if it occurs," says Gil Hobson, vice president, sales and client services for Carolina Logistics Services, Winston-Salem, NC, which provides full-service recall management among its portfolio of reverse logistics services.
"The best first step in planning for a recall is to develop a recall protocol," he adds. "Most companies have a Plan A-that is, they assume they will never have a recall."
Plan B, which too many firms never get around to, says Hobson, includes creation of a detailed, written recall protocol plan and the staging of regular mock recalls to give everyone who might be involved in a recall a chance to practice their roles. These dry runs also provide opportunities to identify weak points or gaps in the plan that should be remedied as soon as possible.
"Multiple people within the organization need to be included in the planning, which means anyone that is part of the supply chain," Hobson adds. This includes logistics, marketing, sales, finance, legal, IT and quality assurance.
From Awareness To Action
There's heightened interest in recall readiness these days among manufacturers and others in the food supply chain, say vendors of systems and services that help companies prepare for and deal with recalls. Yet there are still big gaps between discussion and action.
"A recall is an event that has low probability and high consequences. It is this type of situation that companies tend not to prepare for properly. From that standpoint, the recall process probably is no different today than in the past. If a company has experienced a recall, they are sensitive to the impact it can have and will typically put procedures in place based on what they've learned. However, if they haven't experienced a recall, there is a high probability that they don't have a protocol or plan in place," Hobson observes.
Even companies that have plans in place tend to focus on preventive measures and on public relations approaches for brands under siege, while operational planning regarding the specific how-to's of product identification, location, retrieval and disposition are often overlooked.
"When it comes to recall readiness, we see a high level of interest in the ability to make it happen," adds Vicki Griffith, marketing director, food and beverage for St. Paul, MI-based Lawson Software, "but how to make it happen is still a hodgepodge of processes. The capability is not integrated into the ways people do business."
On a positive note, the nature of companies' questions about recall readiness is changing," observes Rory Granros, director of industry and product marketing for the process industries, with enterprise software developer Infor Global Solutions, Alpharetta, GA.
"Before, questions tended to be very general and simplistic. Now companies are inquiring in more detail about the track and trace capabilities within software packages in ways that reflect a deeper understanding of their needs and the different elements involved."
It's About Accessibility
With the right IT systems in place, a company presented with a single piece of data such as a purchase order, lot or batch number, should be able to identify the location or disposition of every affected product within minutes if not seconds, says Rob Wiersma, Lawson's industry strategy director for food and beverage.
In reality, for many companies today the process takes many hours or days.
"One common point of failure we see is that while the data they need is all there somewhere and all auditable, the amount of time it takes to plow through piles of paper documents or to combine and reconcile different databases in the face of a recall is what puts them at risk," says Infor's Granros.
The continuing trend toward increased outsourcing compounds the problem, he adds, "because now you have to worry about whether you're getting all the information you need from your outsourcing partners as well and how strong are their track and trace capabilities."
Many manufacturers rely on ERP systems for track and trace functionality, only to discover, when faced with a real recall, the information readily available from the system doesn't extend far enough.
"Lot track and trace capability has to be bidirectional," Granros notes. "If you find a problem with a product at the end of the chain, you need to be able to trace that back to the source of supply. If you find a problem in a batch of raw material, you need to trace that forward to every processed product that material has touched. You always want to be able to go from any point in the chain all the way down to the bottom and all the way back up."
The weakness of tracking systems traditionally operated out of ERP platforms is there are too many places where the "chain of custody" of information breaks down.
"If your strategy is to capture manufacturing data in your ERP system, warehouse data in your WMS and shipping information in your transportation system, then when it comes time to trace something, you have to incrementally work through the data in each of those separate repositories. If you need to overlay data from separate systems, or start comparing lists manually, then the process becomes very time consuming and that's where the chain of custody of the data can really start to break down," Granros points out.
Infor's strategy with its Adage enterprise system, is to integrate the ERP platform tightly with the WMS system, sending lot codes into the WMS that accompany the product data all the way through picking and shipping. It then brings the WMS-related data back into the central repository of the ERP. Similarly, Infor offers an integrated PLM application that enables users to start with their own finished products within the ERP database and trace the constituents all the way back up through the procurement chain.
Another of the system's features is its ability to trace sub-lots.
"This is where a lot of meat packers get into problems, when they can't account for 100 percent of the raw material that went into the product they processed. Whether some fell on the floor and was disposed of, or they packaged 99 pounds out of 100 and then did something else with that last pound, the ability to isolate those odds and ends as sub-lots, and show that you actually controlled them, reduces risk and improves your ability to conduct a thorough recall, if need be," Granros points out.
Chad Collins, vice president, global strategy, for Highjump Software, Eden Prairie, MN, observes that its supply chain Advantage suite is "at its core about tracking and tracing products as they move through the supply chain.
"We're not only tracking SKU numbers and quantities as they move in and out of production and distribution and out to the retail locations, we're also tracking a great deal of additional information like lot codes, expiration dates and manufacture dates. We also have the capability to track such data as freeze and thaw cycles.
"And because this capability in the software suite really starts on the supply side, with procurement, we can also track the raw materials or ingredients as they come from suppliers into the production process and trace all of these components back from the finished, delivered product."
Mobile Computing Extends Traceability
The use of mobile computing systems by delivery drivers further extends detailed traceability of products to the actual point of delivery to the retail location, Collins adds.
"With goods that are sensitive to temperature change at particular points in their cycle, for example in bread distribution, this ability to pinpoint and notate every time a product moved from a frozen to an ambient location, can become important as well," Collins notes.
In fact, these sorts of tracking capabilities, Collins and others point out, not only insure a timely response in the event of a recall. They can also become powerful and versatile tools for helping companies improve many aspects of their manufacturing and supply chain processes, by creating rich repositories of historical data linking ingredients, processes and events with specific product outcomes.
For manufacturers that don't have adequate track and trace capabilities built into their ERP and/or supply chain execution suites, another option now available is a separate "track and trace engine," a piece of software designed to gather needed tracking data from among the many disparate systems where it is resides.
One such product is the Lawson M3 Trace Engine, 3.0, a program first developed and utilized in Europe, which has just been introduced in a version designed for the U.S. market.
Lawson's program is a standalone, web-based traceability system that operates with its M3 Enterprise Management system, as well as with many other ERP, farming or food lab software systems available from other vendors.
In addition to helping companies capture and manage tracking information, from procurement of raw materials through production and distribution, the system includes a web-based application for publishing and sharing data such as product origin and transport information online with customers and regulators.
As companies that have been involved in recalls can attest, the ability to communicate accurate, timely data to the public, customers and regulatory authorities can be just as important in preserving brand image as the ability to gather the information and determine the source and scope of the issue.
"This Is Not A Drill"-Be Prepared For The Unexpected
Prior to installing the Highjump Advantage system, Earthbound Farm's trace capabilities were similar to many companies' today.
"Everything was tracked manually on pieces of paper. We had as our goal then to collect all the information within two hours of starting our recall drill. We could typically get there, but it was an extremely labor intensive process. We had to sort through paper bills of lading to identify all the product and where it went, then manually build lists of customers and get the names to sales to contact," explains Will Daniels, vice president of quality, food safety and organic integrity.
"HighJump has enabled us to do all that within minutes of getting a lot or date code. It's also taken much of the potential for user error out of the process. As long as the product scans are accurate and orders are loaded onto the trucks accurately, we have a pretty good chance of making sure that every case gets accounted for and not just what's in our warehouse, but everything that's gone out to customers."
"We can also search for product by pallet, by who handled it, and what line it came from, so we can get much more specific with our recall capabilities than we ever could with our manual process alone," adds Alex Brinsmead, senior software development manager.
"We can pinpoint a particular pallet, or by adding time stamps to our packaging we can get even more specific and narrow down to the precise hour or minute exactly when something was packed, rather than having to look at a whole shift or a whole day's worth of production."
Earthbound Farm installed HighJump in late 2004 with the help of Vitech Business Group, Bellingham, WA, which played a key role in customizing the package for its specific applications. It wasn't long before the system had a chance to prove its track and trace capacity, when in 2006 Earthbound faced a major recall of bagged spinach packed under another brand by its Natural Selection Foods packing company.
"The system provided us with accurate information very quickly. Before, we wouldn't have been able to react as fast. We would have gotten the information together eventually, but it would have taken a lot more time and manpower and been a lot more stressful," Daniels points out.
"With Highjump, once we had the date and lot codes we were looking for, we were able to pull together distribution lists within the hour and that doesn't mean just getting the computer printout, which actually took only minutes," Brinsmead explains.
"That two hours encompassed actually putting everything together, reconciling the production and inventory information with the shipping data, for example, cross-referencing and double-checking everything to make sure all the information was accurate."
Daniel's advice to other companies facing a recall is "Make sure you follow your plan.
"In the chaos of the moment, when you have so many things going on at once, and lots of pressure from different entities both internal and external to make sure action is being taken on a timely basis, you need to make sure you're sticking to your plan as best as possible. So included in your plan should be some form of regular review process to make sure you've covered all the specific points you've written into it when the time comes.
"Preparedness also goes back to making sure every member of the team understands their role and not just from having read it on a piece of paper, but from having had the opportunity to practice their activities in mock recall drills. That also includes talking through the processes in advance and defining common terminologies related to a recall, to make sure that everyone from different segments of the company understands what each other is talking about."
Milking The System
Another organization that's stayed ahead of the curve on recall readiness is Dairy Farmers of America, the giant dairy coop that processes 40 percent of all milk production in the U.S.
"Quality assurance and lot traceability were one of the key reasons we first purchased Infor's Adage system 10 years ago," notes Bill McCurry, supply chain systems manager. The coop has since installed the system in 18 of its operations, and continues to roll it out to additional locations among its total of about 30 manufacturing facilities.
"Where we run the system, the plants are lot-tracking every ingredient and every item of packaging that touch a product. We track vendors' lot numbers as well as our own lot numbers all the way through the manufacturing process, then out to the sales order to identify what customer and ship-to that item went to, all through Infor's Adage ERP system. So at every moment we know what finished goods we have, every vendor item and lot that went into them and where that product is now or has gone." McCurry points out.
In its mock recalls, DFA's quality control group gives plants a two-hour window in which to define all the items in which an ingredient was used, or where a product was shipped to.
"If it's an ingredient where you're putting just a few tablespoons into a big batch, you might use a single lot over as long as a month. It took a long time to track all of that without the system.
"A lot of the plants we roll this into were using notepads and pencils to capture lot information before and thought that adequate, but they're not accustomed to capturing data down to the level of granularity the system provides, or managing inventory by lot codes down to that level of detail. They may know the quantity of sugar they have on hand, for example, but not all the lot numbers each sugar vendor delivered, or what products each of those lots went into.
"It takes a fair amount of training to get your people on the shop floor to record this level of data, and it's almost impossible for them to do so without a system like Infor to track it for you," McCurry notes.
"We co-pack a lot of products and our partners' QC groups will come in to test our recall and tracking capabilities and we've won awards for how quickly we can produce lists, for example, of ever customer that received a product that used a certain vendor's item. The ability to pass those audits with flying colors goes a long way toward helping us sign contracts for the next year," he adds.-C.C.
Outsourcing The Recall Process
While every company is ultimately responsible for its own recall readiness, one option to lessen the burden is outsourcing some or all of the recall planning and/or execution process to a third party.
Carolina Logistics Services, for example, has been managing recalls for clients as part of its portfolio of reverse logistics services since 1985. Its full-service recall management programs range from pre-event services like protocol development and helping companies stage mock recalls, to event management including operating call centers, product retrieval, creating and disbursing returns kits, as well as all other elements that go into the fulfillment/replenishment process.
"We do expect recalls both voluntary and involuntary to increase given the increased regulatory requirements, offshore outsourcing and manufacturers' and retailer's safety concern for their consumers," notes Gil Hobson of CLS, which recently handled over 40 recalls on behalf of manufacturer clients in a single year.
"Reverse logistics is not a core competency of manufacturing firms," he adds. "Given the extreme cost of executing recall events poorly, having an expert partner on board to ensure efficient, cost-effective execution is like a good insurance policy.
Part of what makes recalls difficult for manufacturers, in fact, is their infrequency.
"Recalls are neither predictable, nor repeatable so it requires that a company be able to scale accordingly to handle the increased volume," Hobson points out. "This is a benefit of outsourcing to a third party reverse logistics company that has the experience and resources to be flexible and scale according to the requirements of the situation," he points out.
Manufacturers' forward distribution networks are designed to be effective at processing full-case, first quality goods, he adds. "They don't have the systems, the experience or facilities to deal with the individual items that are returned with a recall. Not to mention that many times the recalled product requires special storage such as a quarantined area to meet regulatory requirements."
Systems to collect and account for the returned products should be automated and capable of providing daily updates not only to meet credit needs, but also to fulfill reporting requirements for government agencies, he notes in addition.
A number of CLS clients were previously involved in recalls that they handled internally and decided to outsource the next time.
"There's so much more regulation and paperwork involved, both in identifying product and in its disposition vs. normal returns, which can overwhelm a distribution center if they don't have a solid plan in place. And in the event of a recall, all this activity is time sensitive. Part of our advantage is the flexibility we have to respond quickly, with approximately 40 warehouses around the country designed to receive returned product, and a field force we can deploy within 24 hours of notification to start going out to stores and pulling product off the shelf. These are not the kinds of activities a manufacturer is set up to respond to quickly," Hobson observes. -C.C.