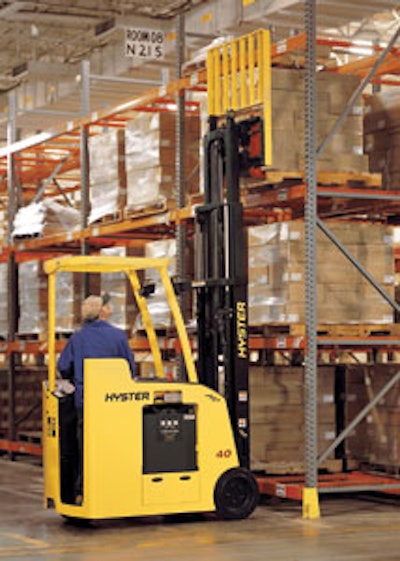
Accidents involving a lift truck and a pedestrian are the most frequently reported and often involve serious or fatal injuries. Hyster Co., Greenville, NC, recently conducted a study of these types of accidents.
Lift truck accident data is published periodically by various sources, including state and federal government organizations. However, specific factual information concerning individual accidents is frequently vague and the factors that contribute to these accidents are difficult to identify.
Hyster's evaluation of its own accident reports indicates that approximately as many of these accidents occurred while the lift truck was traveling forward (including tail-swing accidents) as in reverse. Most reverse travel accidents occurred within the first 10 feet of travel, whereas most of the forward travel accidents occurred after the first 25 feet.
Many of the accidents involved injury to pedestrians who were not only aware of the presence of the lift truck but who were, in fact, working with the operator of the truck that struck them. Hyster found that some lift trucks involved in these accidents were equipped with audible and visible alarms, and that some lift trucks were equipped with alarms which were non-operational at the time of the accidents.
Accident Causes
The lack of detailed information concerning specific accidents makes it impossible to isolate a common or predominant cause of accidents involving a lift truck and a pedestrian. However, some of the factors that may contribute to these accidents include:
• Ambient noise levels;
• Ambient light levels;
• The number of lift trucks and pedestrians present;
• Level of training of lift truck operators;
• Level of education of pedestrians concerning lift truck operating characteristics and how to work around them;
• Physical workplace layout, including separate travel zones for pedestrians and lift trucks;
• Presence of audible or visible warning devices on lift trucks and other mobile equipment in the workplace;
• Presence of audible or visible warning devices on cranes, conveyors or other stationary industrial equipment;
• Lack of specific operating rules for lift truck travel, such as sounding the steering wheel horn at intersections or when changing directions;
• Lack of enforcement by management of safe work procedures for lift truck operators and pedestrians.
Operator, pedestrian training: OSHA regulations require specialized training and regular re-training for lift truck operators and remedial training for operators involved in accidents or near accidents. OSHA estimates that its current operator training requirements will prevent 11 deaths and 9,422 injuries per year.
Pedestrians should understand the operating characteristics of lift trucks when working in their proximity and should follow pedestrian rules that are established for their specific environment by their employers.
Separation of traffic: Unlike automobile and pedestrian traffic, there are no universal "rules of the road" for the manner in which lift trucks and pedestrians interact. Many of the largest and most sophisticated lift truck users have concluded that the most effective way to reduce these accidents is to separate lift truck and pedestrian traffic to the greatest extent possible, using travel lanes dedicated to the trucks and separate travel lanes dedicated to pedestrian traffic.
Travel lanes may be marked with paint on the floor, or separated by physical barriers. Limitations may also be placed in travel areas for lift trucks to keep them away from high-density pedestrian traffic, such as near washrooms, break rooms or time clocks.
Workplace rules to increase safety: Every lift truck application environment is unique. Yet, when it comes to reducing or preventing accidents involving a lift truck and a pedestrian, they all have common resources, including independent safety consultants, and your workers' compensation insurance company's loss control specialists. They can all assist you in developing appropriate rules that may help reduce or prevent the incidence of lift truck/pedestrian accidents in your particular workplace.
Here are some examples of workplace rules that are effective in many applications to reduce or prevent the incidence of lift truck/pedestrian accidents:
• Limit lift truck travel speed;
• Use high visibility work clothes or vests for pedestrians;
• Restrict customers and non-employees from areas where lift trucks may be operating;
• Require lift truck operators to stop and sound the steering wheel horn at intersections or before passing through plastic strip curtains; Require pedestrians not to come closer than a predetermined distance from the lift truck, even when speaking to the operator.
Optional Alarms
Hyster makes available as optional equipment a range of different audible and visible warning devices which you may select for your lift trucks. OSHA regulations and ASME B56.1 safety standards for lift trucks do not require the presence of warning devices on a truck other than the steering wheel horn, which is standard equipment.
Hyster's study of optional warning devices indicates that approximately 70 percent of current lift truck users equip their trucks with some form of audible or visible warning device. However, the available accident data does not show that trucks equipped with optional warning devices are involved in a lower incidence of lift truck/pedestrian accidents than those without them. Many of the largest and most sophisticated users choose not to equip their trucks with such devices.
No manufacturer of audible or visible warning devices has undertaken a study on the effectiveness of their devices in reducing accidents; and no manufacturer could provide Hyster with any data concerning the effectiveness of their devices.
The instructions which accompany such devices instruct the lift truck operator to always look in the direction of travel, regardless of the presence of the device.
In determining whether an audible or visible device may be beneficial in your particular work environment, several factors, including the following, should be considered:
Audible devices: Back-up or motion alarms:
• Sound produced must be loud enough to be heard over other noise in the lift truck operating area;
• Sound should be readily distinguishable from other noise or audible devices in the work area;
• Audible devices may contribute to employee noise exposure and exceed OSHA noise limitation;
• Hearing protection makes it more difficult to hear the audible device and to determine the direction and distance from which the sound is coming;
• Audible devices can be annoying to operators and workers, and may be deactivated;
• Audible devices may also be objectionable to nearby residents.
Visible devices: Flashing, rotating and strobe lights:
• Placement of visible devices must be considered based on use of the lift truck and workplace conditions;
• Lights must clear low overhead obstructions and must not shine or reflect excessively into the operator's eyes;
• Shielding may limit the light's visibility to pedestrians;
• Light color should be different from lights used on stationary equipment or background colors in the workplace;
• Workplace light conditions and reflective surfaces should be considered when selecting the type of light;
• Brightly lighted or outdoor areas may necessitate bright or intense strobe lights, or may make the use of lights ineffective.
Whether an optional warning device may be beneficial overall is dependent on factors specific to your workplace, and may require the assistance of a qualified safety professional to evaluate.
Other considerations: You should always consider the following when using audible and visible warning devices:
• Operators and pedestrians can become accustomed to, and may ignore, visible and audible signaling devices;
• Operators and pedestrians can become dependent on these devices and be less likely to watch for each other;
• Multiple signaling devices in the same area can create confusion or indifference for operators and pedestrians;
• Operations and training should be adjusted to counter these and any other potentially negative effects;
• Constant exposure to these devices can be fatiguing to operators and workers;
• Lift truck users consider the steering wheel horn to be an effective means of warning pedestrians of the presence of a truck.
Assess Your Own Operations
Lift truck users must assess their own workplace to evaluate whether it would be desirable to equip trucks with optional warning devices, and whether it would be desirable to change the layout of the physical workplace. Only you are the expert about your business. You must decide how to equip your lift trucks, based on factors that are unique to your operation.
Safety professionals and workplace safety consultants are available to assist you in making decisions concerning workplace layout and the configuration of lift trucks and other equipment. Insurance companies, industrial safety consultants, workplace safety engineers and other safety professionals should be consulted by anyone who needs assistance in determining how best to meet their specific workplace requirements.