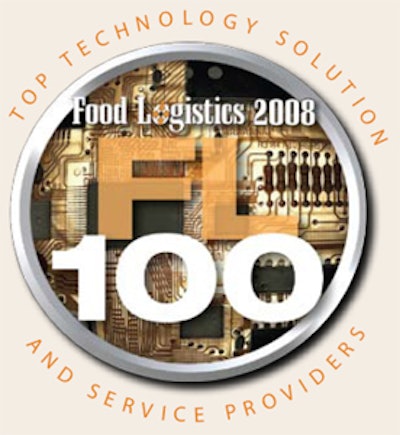
In today's tough economic climate, grocery and foodservice distributors and manufacturers are facing complex distribution challenges and they're applying more technologies to better manage their supply chains.
For the fifth year in a row, Food Logistics has identified the top 100 technology solution and service providers to the food industry.
Known as the FL100, this resource is a listing of software, hardware and IT service providers that focus on the unique needs of food companies. The FL100 are based on their proven track record and expertise in providing food companies with technology and services to help them meet their business objectives.
In this section, we've included a series of charts that list 18 categories of technology solutions and identifies which solution(s) each of the FL100 offers. On the following pages, we list the FL100 with more details, as well as their web addresses.
1SYNC,
Lawrenceville, NJ;
www.1sync.org
Year founded: 2005;
Number of employees: 250;
Number of food customers: NA.
Solution names: 1SYNC Item Management Solution; 1SYNC Price and Promotion Solution; PCATS Gateway Solution; 1SYNC Brand Identity Solution.
Markets served: Manufacturers; supermarket retailers; grocery wholesalers; convenience store distributors; foodservice distributors.
Key problems solved: Reduces out-of-stock volume; reduces new item set-up times; decreases item-maintenance time; reduces invoice discrepancies; higher customer satisfaction.
ABF Freight System Inc.,
Fort Smith, AR;
www.abf.com
Year founded: 1923;
Number of employees: 12,000;
Number of food customers: 100+
Solution names: Shipment Director; Returns Center; Business Trend Analysis; OptiPool; Merge-In-Transit; Supply Chain Services; Reverse Logistics.
Markets served: Manufacturers; supermarket retailers; grocery wholesalers; convenience store distributors; foodservice distributors; third-party logistics providers.
Key problems solved: ABF is consistently recognized for best-in-class performance in productivity, safety and security, loss and damage prevention, yield discipline and electronic and market innovation.
AFS Technologies Inc.,
Phoenix;
www.afsi.com
Year founded: 1985;
Number of employees: 150+;
Number of food customers: 750+
Solution names: AFS Enterprise Resource Planning; Priya Warehouse Management; AFS Order Management System; AFS Driver Delivery System; Discovery Business Intelligence; Compass Forecasting; PromoAssist Trade Promotion Management; Profile Product Database.
Markets served: Manufacturers; supermarket retailers; grocery wholesalers; convenience store distributors; foodservice distributors, third-party logistics providers.
Key problems solved: All AFS solutions are designed to help our food and beverage customers optimize effectiveness, efficiency and profits.
Agentrics,
Chicago,
www.agentrics.com
Year founded: 2005;
Number of employees: 150;
Number of food customers: 60
Solution names: Agentrics GenNovation; Agentrics GenSource; SA2 Worldsync (global data synchronization joint-venture).
Markets served: Manufacturers; supermarket retailers, convenience store distributors; foodservice distributors.
Key problems solved: Agentrics provides a full end-to-end solution for companies looking to improve management of their product development and launching process, sourcing plan for optimal savings, master item data and collaborative forecasting.
*Other solutions/services: eSourcing and supplier discovery services; PLM for private label goods development.
Aldata Solution Inc.,
Atlanta;
www.aldata-solution.com/us
Year founded: 1986;
Number of employees: 543;
Number of food customers: 310 in 53 countries
Solution names: Aldata G.O.L.D. This retail suite includes modules for merchandising, sales, replenishment, logistics and store operations.
Markets served: Supermarket retailers; grocery wholesalers; convenience store distributors.
Key problems solved: Integrated demand and replenishment optimization; store execution; WMS and inventory optimization; item and price management; merchandise management and optimization; supply chain visibility; supplier management; business management and support; retail intelligence and analytics.
ALK Technologies,
Princeton, NJ;
www.alk.com
Year founded: 1979;
Number of employees: 200;
Number of food customers: N/A
Solution names: PC*MILER; PC*MILER/Streets; PC*MILER/HazMat; PC*MILER/Worldwide; PC*MILER/FuelTax.
Markets served: Manufacturers; supermarket retailers; grocery wholesalers; convenience store distributors; foodservice distributors; third-party logistics providers.
Key problems solved: PC*MILER is the industry-standard routing mileage and mapping software. It allows users to guide drivers to delivery locations, verify routes for rating and reporting, get time and cost estimates, streamline the freight payment and audit process, and import locations to customize the database.
Aquitec Inc. (a member of USC Group),
Bagshot, U.K.;
www.aquitecintl.com
Year founded: 1970;
Number of employees: N/A;
Number of food customers: 20
Solution names: SCM Warehouse; SCM Billing; SCM Procurement; SCM/400 WMS; Store Order; Labor Purchasing Management
Markets served: Manufacturers; supermarket retailers; grocery wholesalers; convenience store distributors; foodservice distributors; third-party logistics providers.
Key problems solved: Supply chain costs; supply chain visibility; labor costs; inventory accuracy; service levels; productivity.
ArrowStream Inc.,
Chicago;
www.arrowstream.com
Year founded: 2000;
Number of employees: 80;
Number of food customers: 15+
Solution names: ArrowStream OnDemand.
Markets served: Manufacturers; supermarket retailers; grocery wholesalers; convenience store distributors; foodservice distributors.
Key problems solved: Optimize promotional investment; efficiently manage complex supply chains through visibility of product; build better distribution-chain relationships with automation and synchronized information.
Battery Performance Research Institute,
Alexandria
Bay, NY;
www. batteryperformancereports.com
Year founded: 2001;
Number of employees: 2;
Number of food customers: 12
Solution names: N/A.
Markets served: Manufacturers; supermarket retailers; foodservice distributors.
Key problems solved: Reduce battery room operating costs by doubling battery lifespan. Achieve an eight-month ROI by reducing over-the-road class 8 trucks with no starts and electrical system maintenance costs.
*Other solutions/services: Maximize truck and motive power battery performance
BFC Associates Inc.,
West Chicago, IL;
www.bfcsoftware.com
Year founded: 1984;
Number of employees: 15;
Number of food customers: 100+
Solution names: Dakota Series WMS
Markets served: Manufacturers; grocery wholesalers; convenience store distributors; foodservice distributors.
Key problems solved: Inventory control; elimination of errors; increase in productivity and profitability.
Blinco Systems Inc.,
Toronto;
www.blinco.com
Year founded: 1988;
Number of employees: 16;
Number of food customers: 7
Solution names: 3rdwave GMC
Markets served: Manufacturers; foodservice distributors.
Key problems solved: Improved total business processes delivering significant improvements in inventory management, product cost reduction and operational efficiency. Improved procure to pay visibility and compliance.
*Other solutions/services: Visibility; reporting and analytics; customs.
Blue Sky Technologies Inc.,
Coppell, TX;
www.blueskytech.com
Year founded: 2003;
Number of employees: 10;
Number of food customers: 10
Solution names: Insight; Janus Appointment Management Systems; Insight Truck Tracker
Markets served: Manufacturers; supermarket retailers; grocery wholesalers; convenience store distributors; foodservice distributors; third-party logistics providers.
Key problems solved: Supply chain visibility; key performance indicators; alerting; metrics.
Cadec Global,
Manchester, NH;
www.cadec.com
Year founded: 1976;
Number of employees: 90+;
Number of food customers: 50+
Solution names: Mobius TTS; PowerVue
Markets served: Manufacturers; supermarket retailers; grocery wholesalers; convenience store distributors; foodservice distributors; third-party logistics providers.
Key problems solved: Helps extend supply chain into truck cabs. Monitors driver behaviors such as speeding, sudden decels, excessive idling, off-route driving to improve safety and reduce fuel consumption. Real-time cold chain management to preserve food in transport.
CAMS Software Corp.,
New Westminster, British Columbia, Canada;
www.camspro.com
Year founded: 1997;
Number of employees: 15;
Number of food customers: 20
Solution names: CAMS Professional; CAMS Backhaul Module; CAMS Service Manager
Markets served: Supermarket retailers; grocery wholesalers.
Key problems solved: Online visual dispatch optimization; driver payroll, hourly and/or activity-based pay; backhaul and salvage optimization; transportation reporting; equipment utilization.
CaseStack Inc.,
Santa Monica, CA;
www.casestack.com
Year founded: 1999;
Number of employees: 100+;
Number of food customers: 500+
Solution names: Retailer Consolidation Program; Transportation Brokering
Markets served: Manufacturers.
Key problems solved: Save time and money for mid-sized companies with high frequency and low volume orders. Minimize carbon footprint and wasteful shipping practices through retailer consolidation programs. Manage inventory expansions.
CDC Software,
Atlanta;
www.cdcsoftware.com
Year founded: 1999;
Number of employees: 2,000;
Number of food customers: 431
Solution names: CDC Factory; Ross ERP and SCM; e-M-POWER; CDC Supply Chain; Respond; c360 CRM add-on products.
Markets served: Manufacturers; supermarket retailers; grocery wholesalers; convenience store distributors; foodservice distributors; third-party logistics providers.
Key problems solved: Depending on the product line addressed, each suite offers a range of benefits and addresses key problems.
ClearOrbit,
Austin, TX;
www.clearorbit.com
Year founded: 1994;
Number of employees: 150;
Number of food customers: 6
Solution names: Supplier Collaboration for Oracle: Xtended Process Control (X.PC); Mobile Applications for Oracle: Gemini Simplified Interface (G.SI) Suite; OPM Data Collection: Gemini Simplified Interface (G.S1) for Receiving, Inventory, Manufacturing, Shipping and QA for OPM; Bar-Code and RFID Printing: Compliance Label Manager (CLM); Enterprise Returns Management (ERM); Supply Network Gateway (SNG).
Markets served: Manufacturers; foodservice distributors; third-party logistics providers.
Key problems solved: ClearOrbit solutions leverage and extend enterprise systems internally and in collaboration with trading partners to optimize operations, eliminate errors and reduce latency in inventory flow to respond to real-time demand change.
CLS Inc. (an Inmar company),
Winston-Salem, NC;
www.cls.inmar.com
Year founded: 1985;
Number of employees: NA;
Number of food customers: 200+
Solution names: Retailer and manufacturer solutions include Returns Management; Asset Recovery; Risk Management; Returns Prevention; Information Intelligence.
Markets served: Manufacturers; supermarket retailers; grocery wholesalers; convenience store distributors.
Key problems solved: Returns Management (both RX and Front Store)--single source solution from return authorization to final disposition, including facility management, processing of physical returns, debit and credit financial management, reverse to forward, and policy consulting; Asset Recovery--value-added liquidation for discontinued, overstocks, withdrawn, surplus, closeouts, salvage, obsolete and distressed inventory balanced between optimal revenue maximization and brand and channel protection; Risk Management--regulatory compliant disposition, recall management including notification, product retrieval and payment and counterfeit detection and monitoring for brand protection and supply chain integrity; Returns Prevention--supply chain analysis for returns reduction and avoidance, best practices, score carding and packaging analysis at all touch points including manufacturer plant, distribution center, retailers' regional distribution center and retail store.
Container and Pooling Solutions (CAPS),
Livonia, MI;
www.useCAPS.com
Year founded: 1998;
Number of employees: 20;
Number of food customers: 50
Solution names: CAPS-135 Liquid Container; CAPS-TRAC Suite - Tracking Software
Markets served: Third-party logistics providers.
Key problems solved: Container loss - our containers are all bar coded and tracked via our proprietary CAPS-TRAC tracking software, reducing the risk of loss. Reduce cost - CAPS container rental and tracking typically saves our customers 10-15 percent off their current packaging spending. Save storage space - CAPS' containers are collapsible, saving valuable storage space once containers have been emptied. Additionally, collapsibility allows for more containers per truck, ultimately reducing freight costs; reduce risk of contamination - with liners being disposed of after every use, there's no risk of product contamination. Environmentally friendly - because containers are rented and used multiple times, they are more environmentally friendly than corrugated containers as they do not require disposal. Additionally, once a container can no longer be used, it is reground and the plastic materials are recycled and reused. Less residual and harborage points - containers have smooth surfaces for optimal hygiene and a sump to ensure less residual (wasted product). Eliminate the need for strapping and pallets - saving money and reducing disposal fees. No racking required. Hold 315-gallons - CAPS-315 has the largest weight capacity of any plastic collapsible liquid container (3,307 lbs).
Daifuku Co. Ltd.,
Osaka, Japan;
www.daifukuamerica.com
Year founded: 1937;
Number of employees: 5,663;
Number of food customers: 5,325+
Solution names: Automated Storage & Retrieval Systems (AS/RS); Sorting & Picking Systems (including Sorting Transfer Vehicles); Conveyor & Vehicle Systems; Containers & Carts; Warehouse Management & Control Software
Markets served: Manufacturers; supermarket retailers; grocery wholesalers; convenience store distributors; foodservice distributors; third-party logistics providers.
Key problems solved: We help companies recapture floor space, reduce errors, streamline processes, decrease cycle time and improve productivity.
*Other solutions/services: Automated storage and retrieval systems (AS/RS).
Deacom Inc.,
Wayne, PA;
www.deacom.net
Year founded: 1995;
Number of employees: 15;
Number of food customers: 2
Solution names: Deacom Integrated Accounting and Enterprise Resource Planning (ERP) Software System.
Markets served: Manufacturers.
Key problems solved: Establish data integrity throughout its business; create company-wide control process controls; minimize user training across the company, from the novice to the sophisticated user.
DemandTec Inc.,
San Carlos, CA
www.demandtec.com
Year founded: 1999;
Number of employees: 270;
Number of food customers: 140
Solution names: For Retail: Lifecycle Price Optimization; End-to-End Promotion Management; Assortment and Space; Targeted Marketing. For Consumer Products: Trade Effectiveness
Markets served: Manufacturers; supermarket retailers; grocery wholesalers; convenience store distributors; foodservice distributors.
Key problems solved: DemandTec enables retailers and consumer products companies to optimize merchandising and marketing decisions, individually or collaboratively, to achieve their sales volume, revenue and profitability objectives. *Other solutions/services: Price, promotion and assortment optimization and deal management.
Dematic Corp.,
Grand Rapids, MI;
www.dematic.us
Year founded: 1939;
Number of employees: 1,300;
Number of food customers: >50
Solution names: CL-100 conveyor; SL-300 sortation; PickDirector; SortDirector
Markets served: Manufacturers; supermarket retailers; grocery wholesalers; convenience store distributors; foodservice distributors; third-party logistics providers.
Key problems solved: Store-friendly deliveries; SKU proliferation; increased accuracy and productivity.
Descartes Systems Group,
Waterloo, Ontario, Canada;
www.descartes.com
Year founded: 1981;
Number of employees: 350+;
Number of food customers: NA
Solution names: Descartes Delivery Management Suite
Markets served: Manufacturers; supermarket retailers; grocery wholesalers; convenience store distributors; foodservice distributors; third-party logistics providers.
Key problems solved: Create engineered plans; benchmark driver and customer performance; provide dynamic route optimization and optimal route sequencing; monitor on-time delivery performance; improve customer service, through proactive customer notification and exception management in the field.
Echo Global Logistics,
Chicago;
www.echo.com
Year founded: 2004;
Number of employees: 435;
Number of food customers: 30
Solution names: Total Logistics Management
Markets served: Manufacturers; supermarket retailers; grocery wholesalers; convenience store distributors; foodservice distributors.
Key problems solved: Echo is a technology-based transportation management company that leverages the transportation spend of our more than 7,000 clients to create bottom-line cost savings for our clients.
EPIC Group--Global Technology,
St. Charles, IL;
www.epicglobaltech.com
Year founded: 2000;
Number of employees: 11;
Number of food customers: 14
Solution names: Hawkeye Perfect Measure Systems
Markets served: Manufacturers; grocery wholesalers; foodservice distributors; third-party logistics providers.
Key problems solved: Retailers and manufacturers: Eliminates follow on trucks to stores for when a pallet or tote does not fit due to erroneous weight or cube; perfect slot selection in the warehouse; eliminates costly state fines for overweights. For shelf management systems and category management: perfect measurements allow perfect shelf plans that fit all products at retail.
*Other solutions/services: Dimension measuring; cubing; space management.
Eqos Inc.,
Burlington, MA;
www.eqos.com
Year founded: 1997;
Number of employees: 60;
Number of food customers: NA
Solution names: Eqos Enterprise and Eqos FastTrack Sourcing
Markets served: Manufacturers; supermarket retailers.
Key problems solved: Eqos FastTrack is the industry's first "one-stop" solution designed to unite and streamline retail sourcing operations across buying teams, including agents and suppliers, both locally and globally. This web-based, fully hosted and supported solution supports multi-category retail businesses and is deployable within 30 days. Designed to deliver increased margins, decreased product lead times, reduced risk of non-compliance and improved customer loyalty, FastTrack provides smart sourcing for a monthly fee.
Galleria Retail Technology Solutions,
Chicago;
www.galleria-rts.com
Year founded: 1989;
Number of employees: 70;
Number of food customers: 9
Solution names: Galleria's Version 7 Customer-Centric Merchandising Solution
Markets served: Manufacturers; supermarket retailers; grocery wholesalers.
Key problems solved: Food retailers are constantly striving to put the optimal products in the optimal quantity on their shelves to meet consumer demand and maximize sales. Galleria's Version 7 customer-centric merchandising solution solves this problem by generating merchandise plans that allow retailers to get the right product to the right store, in the right capacity at the right time. By doing so, retailers are able to optimize inventory on the selling floor to improve availability and reduce wastage. Also, because no store is the same, the solution combines centralized control and localized influence to ensure that demand is met on a story-by-store basis to eliminate wasted space and excess inventory.
GlobeRanger Corp.,
Richardson, TX,
www.globeranger.com
Year founded: 1999;
Number of employees: 50;
Number of food customers: 5
Solution names: RFID Food and Perishable Track and Trace Visibility Solution
Markets served: Supermarket retailers; grocery wholesalers; convenience store distributors; foodservice distributors; third-party logistics providers.
Key problems solved: Completes real-time monitoring of complete harvest, manufacturing to retail food supply chain processes; controls outbreaks of health and safety breaches to the perishable supply chain.
HighJump Software,
Eden Prairie, MN
www.highjump.com/FoodLogistics
Year founded: 1983;
Number of employees: 250;
Number of food customers: N/A
Solution names: HighJump Supply Chain Advantage
Markets served: Manufacturers; supermarket retailers; grocery wholesalers; convenience store distributors; foodservice distributors; third-party logistics providers.
Key problems solved: Intense competition, changing regulations, slim margins, safety and quality of inventory.
HK Systems,
Milwaukee, WI;
www.hksystems.com
Year founded: 1993;
Number of employees: 1,200;
Number of food customers: 100+
Solution names: Automated Material Handling Systems.
Markets served: Manufacturers; supermarket retailers; grocery wholesalers; convenience store distributors; foodservice distributors; third-party logistics providers.
Key problems solved: Products and material movement of pallets, cases or eaches; automated storage and retrieval of pallets, cases or eaches; warehouse management and equipment control.
IBM Corp.,
Armonk, NY;
www.ibm.com
Year founded: 1896;
Number of employees: 380,000+;
Number of food customers: N/A
Solution names: Many, including hardware, software and business partners
Markets served: Manufacturers; supermarket retailers; grocery wholesalers; convenience store distributors; foodservice distributors; third-party logistics providers.
Key problems solved: Grow revenue, cut costs, create a more sustainable supply chain, enhance corporate social responsibility, grow customer loyalty and drive innovation.
I.D. Systems Inc.;
Hackensack, NJ;
www.id-systems.com
Year founded: 1993;
Number of employees: 108;
Number of food customers: 7
Solution names: Wireless Asset Net wireless control, tracking and management of material handling vehicles and the people who operate them.
Markets served: Manufacturers; supermarket retailers; grocery wholesalers; convenience store distributors; foodservice distributors; third-party logistics providers.
Key problems solved: Increased productivity and vehicle utilization; decreased capital and operating costs; improved safety practices and regulatory compliance; reduced damage caused by industrial trucks.
Infor,
Alpharetta, GA;
www.infor.com
Year founded: 2002;
Number of employees: 9,000;
Number of food customers: 1,200
Solution names: Infor PLM Optiva; Infor ERP Adage; Infor ERP LX; Infor SCM Advanced Scheduling; Infor SCM Advanced Planning; Infor SCM Demand Planning; Infor EAM Be
Markets served: Manufacturers; supermarket retailers; foodservice distributors.
Key problems solved: S&OP to improve product and customer profitability; inventory optimization to meet SLA with less inventory; lowest total delivered cost optimization; carbon footprint optimization; optimized plant scheduling; minimize total cost of service with promotions; lowest total cost of quality with lot track/trace and actual costing.
*Other solutions/services: Product Lifecycle Management.
INSIGHT Inc.,
Manassas, VA;
www.insight-mss.com
Year founded: 1978;
Number of employees: 30;
Number of food customers: 32
Solution names: Sails 21.
Markets served: Manufacturers; foodservice distributors; third-party logistics providers.
Key problems solved: Supply chain network design; AC audits; SC security; greening of the supply chain; planning and scheduling; site selection; mergers and acquisitions.
*Other solutions/services: Advanced planning and scheduling.
Infratab Inc.,
Oxnard, CA;
www.infratab.com
Year founded: 2003;
Number of employees: 15;
Number of food customers: 5
Solution names: Infratab Freshtime EPC RFID Gen 2 Labels and Tags
Markets served: Manufacturers; grocery wholesalers; convenience store distributors; foodservice distributors; third-party logistics providers.
Key problems solved: Provide a true indication on a 100-point scale of the status of a products' abuse due to temperature over time--this is a real-time condition status along with the EPC RFID number; provide a unique transfer from the pallet to the individual sub-pallet of any number of cases or items for a mixed lot with new labels that continue the monitoring.
Interlink Technologies,
Perrysburg, OH;
www.thinkinterlink.com
Year founded: 1986;
Number of employees: NA;
Number of food customers: NA
Solution names: WHSe-LINK
Markets served: Manufacturers; grocery wholesalers; foodservice distributors; third-party logistics providers.
Key problems solved: Real-time inventory accuracy; recalls and audits managed easily; manage and track lot/batch/serial; manage expiration dates and environmental controls; capture catch weight; eliminate shipping errors; multiple receiving methods; directed putaway; multiple pick methods; reduced cycle time; system security; productivity tools; inquiries and reports; short learning curve; integration with other business systems.
iTradeNetwork (ITN),
Pleasanton, CA;
www.itradenetwork.com
Year founded: 1999;
Number of employees: 275;
Number of food customers: 5,500+
Solution names: On-demand supply chain management and intelligence solutions for the food industry including: Procurement; Contract Management; Transportation and Logistics; Data Synchronization and Enrichment; Sales Insight; Spend Management; Quality Management.
Markets served: Manufacturers; supermarket retailers; grocery wholesalers; convenience store distributors; foodservice distributors; third-party logistics providers.
Key problems solved: iTradeNetwork's solutions enable all supply chain players--distributors , manufacturers, operators and retailers--to operate their businesses more profitably and efficiently.
JDA Software Group Inc.,
Scottsdale, AZ;
www.jda.com
Year founded: 1985;
Number of employees: 1,700+;
Number of food customers: 1,500
Solution names: JDA Space & Category Management Solutions; JDA Price & Promotion Management Solutions; JDA Demand; JDA Allocation & Replenishment solutions; JDA Supply & Manufacturing Management Solutions; JDA Collaboration Solutions; JDA Transportation & Logistics Management Solutions; JDA Store Systems Solutions; JDA Merchandise Operations Solutions
Markets served: Manufacturers; supermarket retailers; grocery wholesalers; convenience store distributors; foodservice distributors; third-party logistics providers.
Key problems solved: Customer relationship management; data synchronization; demand management; inventory control; load planning; mobile technology; reverse logistics; routing and scheduling; supply chain management; 3PL; transportation management; warehouse management.
John Galt Solutions Inc.,
Chicago;
www.johngalt.com
Year founded: 1996;
Number of employees: 35;
Number of food customers: 250+
Solution names: ForecastX Wizard; Atlas Planning Suite; Consumer Centric Planning.
Markets served: Manufacturers.
Key problems solved: Produce accurate and timely demand forecasts, collect input from collaborative partners, produce inventory plans.
JTS (Johanson Transportation Service), Fresno, CA;
www.johansontrans.com
Year founded: 1971; Number of employees: 60; Number of food customers: 500+
Solution names: Domestic services; technology, consulting
Markets served: Manufacturers; supermarket retailers; grocery wholesalers; convenience store distributors; foodservice distributors.
Key problems solved: Streamlines supply chain communications; integrate point-to-point systems to unify technology solutions; offer access and visibility into logistics process and real-time tracking of shipments; offer connectivity to exchange business data electronically with minimal manual intervention; reduce time, errors, costs associated with manual order processing.
Kelron Logistics,
Mississaugua, Ontario, Canada;
www.kelron.com
Year founded: 1992;
Number of employees: NA;
Number of food customers: NA
Solution names: Freight Management, Transportation; Warehousing/Distribution
Markets served: Manufacturers; supermarket retailers; grocery wholesalers; convenience store distributors; foodservice distributors.
Key problems solved: Inventory control; load planning; reverse logistics; routing/scheduling; supply chain management; third-party logistics; trade compliance; transportation management; warehouse management; yard management.
LANSA Inc.,
Downers Grove, IL;
www.lansa.com
Year founded: 1987;
Number of employees: 225;
Number of food customers: 330
Solution names: LANSA Data Sync Direct
Markets served: Manufacturers; supermarket retailers; grocery wholesalers; convenience store distributors; foodservice distributors.
Key problems solved: LANSA Data Sync Direct provides a complete end-to-end solution for manufacturers and suppliers who need to be compliant with the Global Data Synchronization (GDS) initiative. The solution's primary objective is to provide easy-to-use management of a few (or thousands) of Global Trading Item Numbers (GTINs).
LANSA Data Sync Direct allows suppliers, distributors and manufacturers to access and update Item information stored in their existing ERP system and securely send it to a certified data pool of their choice. LANSA Data Sync Direct can be integrated with over 20 of the most popular ERP solutions using a simple mapping module concept. No additional software or outsourcing services are required. LANSA Data Sync Direct is installed on the enterprise's production server or can be delivered as an appliance bundled with a Windows or Linux server. A hosted version is also available on a subscription basis.
Lawson Software,
St. Paul, MN;
www.lawson.com
Year founded: 1975;
Number of employees: 4,200;
Number of food customers: 400
Solution names: Analytics for Food and Beverage; Planning Workbench for Food and Beverage; Lawson Stock Build Optimizer for Food and Beverage; Business Intelligence; Trace Engine; Supply Chain Management; Manufacturing Operations; Financial Management; Sales and Marketing Automation; Human Capital Management; Enterprise Asset Management.
Markets served: Manufacturers; foodservice distributors.
Key problems solved: Traceability; livestock management; supply chain management; forecasting and planning; plant maintenance; performance management; customer sales and service; manufacturing operations.
LeanLogistics,
Holland, MI;
www.leanlogistics.com
Year founded: 1999;
Number of employees: 75;
Number of food customers: 20
Solution names: LeanLogistics On-Demand TMS; LeanLogistics WebSettle; LeanLogistics Supplier Inbound Management; LeanLogistics Private Transportation Marketplace
Markets served: Manufacturers; supermarket retailers; grocery wholesalers; foodservice distributors; third-party logistics providers.
Key problems solved: On-Demand TMS provides complete daily planning, execution and settlement functions in addition to the periodic strategic procurement functions. It also provides unique functions that can only be delivered through a network: supplier inbound management, appointment scheduling, benchmarking and network-wide reporting, a private transportation marketplace to obtain capacity and lower costs and total supply chain visibility.
Logility Inc.,
Atlanta;
www.logility.com
Year founded: 1996;
Number of employees: 141;
Number of food customers: 28 percent of customer base
Solution names: Logility Voyager Solutions
Markets served: Manufacturers; grocery wholesalers; foodservice distributors.
Key problems solved: Eliminate supply chain problems caused by limited visibility, errors, incomplete data and delayed communications; optimize production in multiple plants by managing capacity constraints, changeovers, shelf-life limitations, safety requirements and more; plan and manage promotions by modeling multiple demand factors; streamline sales and operations planning; satisfy retailer requirements such as Vendor Managed Inventory (VMI); lower transportation costs and increase movement efficiencies.
Lucas Systems Inc.,
Pittsburgh;
www.lucasware.com
Year founded: 1998;
Number of employees: 50;
Number of food customers: 18
Solution names: Jennifer
Markets served: Manufacturers; supermarket retailers; grocery wholesalers; convenience store distributors; foodservice distributors; third-party logistics providers.
Key problems solved: Jennifer improves order selection accuracy and productivity by creating a hands- and eyes-free selection process using voice technology running on industry-standard mobile RF terminals.
Manhattan Associates Inc.,
Atlanta;
www.manh.com
Year founded: 1992;
Number of employees: 2,200;
Number of food customers: 50
Solution names: Distribution Management; Transportation Lifecycle Management; Order Lifecycle Management; Inventory Optimization and Planning and Forecasting
Markets served: Manufacturers; supermarket retailers; grocery wholesalers; convenience store distributors; foodservice distributors; third-party logistics providers.
Key problems solved: Out-of-stock issues; freshness; DC to shelf; inventory control.
MicroAnalytics Inc.,
Arlington, VA
www.bestroutes.com
Year founded: 1983;
Number of employees: 20;
Number of food customers: 80+
Solution names: TruckStops Vehicle Routing Software; OptiSite Distribution Planning Software
Markets served: Manufacturers; supermarket retailers; grocery wholesalers; convenience store distributors; foodservice distributors; third-party logistics providers.
Key problems solved: Routing and scheduling; supply chain management; transportation management; warehouse management.
*Other solutions/services: Distribution planning.
Motorola,
Schaumburg, IL;
www.motorola.com
Year founded: 1928;
Number of employees: 60,000+;
Number of food customers: 1,150+
Solution names: MC70 Series; VC5000 Series; RFID; Wireless Infrastructure; MSP (Mobility Services Platform).
Markets served: Manufacturers; supermarket retailers; grocery wholesalers; convenience store distributors; foodservice distributors; third-party logistics providers.
Key problems solved: Demand management; inventory control; load planning; mobile technology; RFID; supply chain management; 3PL; transportation management; warehouse management; wireless technology; yard management.
Next Generation Logistics Inc.,
Inverness, IL
www.nextgeneration.com
Year founded: 1988;
Number of employees: 17;
Number of food customers: 1,300
Solution names: FreightMaster TMS Transportation Management System; FreightMaster AMS Appointment Management System; NEXTrack Internet Collaboration Portal; NEXTStop Bid Exchange Portal
Markets served: Manufacturers; supermarket retailers; grocery wholesalers; foodservice distributors; third-party logistics providers.
Key problems solved: Efficient transportation procurement; reduction in costs; increase in on-time performance.
O4 Corp.,
Atlanta;
www.O4corporation.com
Year founded: 1998;
Number of employees: 70+;
Number of food customers: 50+
Solution names: O4 Software Solution for Retail Execution
Markets served: Manufacturers; foodservice distributors.
Key problems solved: This is next-generation mobile computing technology that enables: faster, more ergonomic user interfaces; faster and more reliable order processing and reporting speeds; a complete solution that integrates route accounting with merchandising applications; flexibility to tailor the applications to each company's specific business processes and workflows; flexible reporting capabilities; global translations to any currency or language.
Optiant,
Burlington, MA;
www.optiant.com
Year founded: 2000;
Number of employees: 20;
Number of food customers: 5
Solution names: PowerChain Network Design; PowerChain Inventory; PowerChain Planner
Markets served: Manufacturers.
Key problems solved: Inventory management, planning and control; strategic and tactical network design; multi-echelon inventory optimization; maintain stock level and costs at optimal levels; establish inventory policies; pool inventory to minimize risk; supply chain scenario and sensitivity analysis; supply chain modeling and visualization; multi-centric, multi-model measurement, reporting and analysis on executive dashboards.
ORTEC,
Atlanta;
www.us.ortec.com
Year founded: 1981;
Number of employees: 700;
Number of food customers: 20+
Solution names: Logistics Execution Optimizer-LEO; ORTEC Routing; ORTEC Routing; ORTEC Loading; ORTEC Transport and Distribution; ORTEC Service Planning; ORTEC Workforce Scheduling
Markets served: Manufacturers; supermarket retailers; grocery wholesalers; convenience store distributors; foodservice distributors; third-party logistics providers.
Key problems solved: Resource utilization; warehouse labor efficiency; customer service levels; mileage reduction; resource reduction; overall transportation spend.
PakSense,
Boise, ID;
www.paksense.com
Year founded: 2005;
Number of employees: 17;
Number of food customers: 500
Solution names: PakSense Ultra Contact Label; PakSense Ultra T3
Markets served: Manufacturers; supermarket retailers; grocery wholesalers; convenience store distributors; foodservice distributors; third-party logistics providers. Key problems solved: Farm-to-fork traceability; integrated temperature monitoring; COOL (Country of Origin Labeling) capabilities in a single solution.
*Other solutions/services: Trace forward/trace back.
Paragon Software Systems,
Dallas;
www.paragonrouting.com
Year founded: 1991;
Number of employees: 50;
Number of food customers: 75+
Solution names: Paragon Routing and Scheduling Optimizer; Paragon Multi Depot; Paragon Integrated Fleets; Paragon Fleet Controller; Paragon Home Delivery System; Paragon Fastnet; Paragon Multi Period Planner; Paragon Territory Optimizer; Paragon Fixed Route Manager; Paragon Carbon Minimizer.
Markets served: Manufacturers; supermarket retailers; grocery wholesalers; convenience store distributors; foodservice distributors; third-party logistics providers.
Key problems solved: Paragon software is used for routing and scheduling optimization on a daily basis; managing transportation resources; rationalizing fixed routes; strategic planning and modeling; scheduling home deliveries continuously as orders are being confirmed; and managing the execution of the transportation plan in real time using truck tracking technology.
PeopleNet,
Chaska, MN;
www.peoplenetonline.com
Year founded: 1994;
Number of employees: 190;
Number of food customers: 400
Solution names: PeopleNet g3 Onboard Computer, Mobile Communications and Fleet Management System; PeopleNet BLU Driver Display.
Markets served: Manufacturers; supermarket retailers; grocery wholesalers; convenience store distributors; foodservice distributors; third-party logistics providers.
Key problems solved: Compliance; safety; fuel economy; driver productivity; route efficiency.
*Other solutions/services: EOBR; compliance solutions; automated fuel tax; accident reconstruction; driver training videos.
PINC Solutions,
Berkeley, CA;
www.pincsolutions.
com
Year founded: 2004;
Number of employees: 30;
Number of food customers: 10+
Solution names: Yard Hound; Yard Hound Reefer
Markets served: Manufacturers; supermarket retailers; grocery wholesalers; convenience store distributors; foodservice distributors; third-party logistics providers.
Key problems solved: Lack of real-time visibility (i.e. accurate and timely information) into the key linkages of the food supply chain in the yards (at DCs/warehouses, plants, stores, etc): automated yard info collection--eliminating time-consuming manual yard audits; real-time information sharing across organizations within a company--increase visibility for (geographically diverse) departments involved in transportation logistics planning and management; improve communication among yard and DC personnel--reduced unproductive administrative time; better asset and resource utilization--increase operational efficiency and reduce costs; enable fact-based decision making--provide actionable information for business process optimization and redesign RFID; transportation management; yard management.
QAD Inc.,
Santa Barbara, CA;
www.qad.com
Year founded: 1976;
Number of employees: 1,600;
Number of food customers: 300
Solution names: QAD Enterprise Applications 2008
Markets served: Manufacturers; third-party logistics providers.
Key problems solved: QAD Enterprise Applications delivers a powerful combination of technology and pre-integrated business applications built specifically to address issues facing the food and beverage industry.
QUALCOMM,
San Diego;
www.qualcomm.com
Year founded: 1985;
Number of employees: 1,000;
Number of food customers: 25
Solution names: OmniVision Transportation Services including mobile computing platform; messaging; hours of service; arrival and departure notification
Markets served: Manufacturers; supermarket retailers; grocery wholesalers; convenience store distributors; foodservice distributors; third-party logistics providers.
Key problems solved: Driver productivity and operational efficiency as related to delivery of goods; improvement in transportation-related safety; transportation related regularoty compliance.
Real Time Freight Services LLC,
Chicago
www.realtimefreight.com
Year founded: 2003;
Number of employees: 45;
Number of food customers: 5,000
Solution names: RTF Shipper Edition; RTF Carrier Edition; RTF Exchange Edition
Markets served: Manufacturers; supermarket retailers; grocery wholesalers; convenience store distributors; foodservice distributors; third-party logistics providers.
Key problems solved: Our customers realize a centralized, secure, controlled freight management solution. Increased efficiency is achieved at many levels from saving time and money with our closed loop architecture. Our shipper clients have the ability to scale capacity with the ability to access over 15,000 transportation members. The many advantages of a Real Time Freight membership include the reallocation of resources and lower freight spend. Real Time Freight eliminates information silos to help companies centralize and share information to help them make better and more informed decisions for today and for the future. Real Time Freight also provides the ability for shippers to track their freight as well as run sophisticated reports.
RedPrairie Corp.,
Waukesha, WI;
www.redprairie.com
Year founded: 1975;
Number of employees: 1,300;
Number of food customers: 100+
Solution names: Warehouse Management; Workforce Management; Financial Management; Inventory Management; Execution Management; Learning Management; Performance Management; Transportation Management; Food Processing; Error Proofing/Traceability; Sequence Delivery; Build-to-Order; Supply Chain Visibility; Dashboards
Markets served: Manufacturers; supermarket retailers; grocery wholesalers; convenience store distributors; foodservice distributors; third-party logistics providers.
Key problems solved: The RedPrairie suite of solutions seamlessly orchestrates all supply chain execution functions in real time--giving organizations an end-to-end view of raw materials, warehoused goods, moving inventory and merchandise on store shelves. These capabilities enable firms to reallocate inventory on the fly, to meet changing customer needs without unnecessary disruption, to better manage transportation costs and to ensure product freshness and safety. The results are reduced inventory levels at each stage, improved on-shelf and just-in-time performance, and improved top line growth and profitability.
Retalix USA,
Plano, TX,
www.retalix.com
Year founded: 1982;
Number of employees: 1,500+;
Number of food customers: 1,000+
Solution names: Power Suite of Products--Enterprise, Demand Planning, WMS, Delivery, Sell, Net, Analyzer; Transportation--Traffic Management, Dock Scheduling, Yard Management; SMC Suite of Products--Biceps, Triceps, Abs, Prompt; Store Suite of Products--Loyalty, Fuel, POS, Kiosk, Front Office, Store Replenishment
Markets served: Manufacturers; supermarket retailers; grocery wholesalers; convenience store distributors; foodservice distributors; third-party logistics providers.
Key problems solved: Retalix solves problems related to enterprise data, inventory investment, freight costs, labor productivity, order entry, analyzing supply chain data and managing store operations.
*Other solutions/services: PDA delivery; business intelligence.
Revionics Inc.,
Granite Bay, CA;
www.revionics.com
Year founded: 2002;
Number of employees: 70;
Number of food customers: 110
Solution names: Revionics Advanced Pricing System (RAPS)
Markets served: Supermarket retailers; grocery wholesalers; convenience store distributors; foodservice distributors.
Key problems solved: We help our customers maximize revenue, margin and productivity by leveraging demand intelligence and advance pricing science.
*Other solutions/services: Price, promotion and markdown optimization.
Robocom Systems,
Farmingdale, NY;
www.robocom.com
Year founded: 1982;
Number of employees: 50;
Number of food customers: 20
Solution names: ROC WMS; RIMS WMS; R-Labor, Labor Management System; R-Voice, Voice Picking System; Star TMS; R-Webstore
Markets served: Manufacturers; supermarket retailers; grocery wholesalers; convenience store distributors; foodservice distributors; third-party logistics providers.
Key problems solved: Lot traceability; Country of Origin Label (COOL) compliance; attainment of high levels of inventory accuracy; integration of warehouse, transportation, labor and voice applications designed to improve performance.
Royal 4 Systems Inc.,
Long Beach, CA;
www.royal4.com
Year founded: 1984;
Number of employees: 42;
Number of food customers: 40
Solution names: Royal 4 ERP System; W.I.S.E. WMS System
Markets served: Manufacturers; supermarket retailers; grocery wholesalers; convenience store distributors; foodservice distributors; third-party logistics providers.
Key problems solved: Royal 4 Systems is a leader in providing both WMS and ERP technologies that an be used separately or combined to create a powerful supply chain solution for the food and beverage industry.
Ryder,
Miami;
www.ryder.com
Year founded: 1933;
Number of employees: 28,800;
Number of food customers: NA
Solution names: Supply Chain Solutions; Transportation Solutions; Warehousing and Value-Added Solutions; Dedicated Contract Carriage; Fleet Management Solutions
Markets served: Manufacturers; supermarket retailers; grocery wholesalers; convenience store distributors; foodservice distributors; third-party logistics providers.
Key problems solved: Inventory control; load planning; mobile technology; RFID; reverse logistics; routing and scheduling; supply chain management; 3PL; transportation management; warehouse management; wireless technology; yard management.
SAF USA Inc.,
Grapevine, TX;
www.saf-usa.com
Year founded: 1996;
Number of employees: 150+;
Number of food customers: 20
Solution names: SAF SuperStore; SAF SuperWarehouse; SAP SuperForecast
Markets served: Manufacturers; supermarket retailers; grocery wholesalers; convenience store distributors.
Key problems solved: SAF USA helps retailers and manufacturers overcome competition in the retail market by delivering automated demand forecasting and computer generated ordering (CGO) software solutions. By using SAF's software to automatically determine inventory positions, demand forecasts and optimal orders, users can ensure that the right products are always available in the required quantity. Doing so results in reduced inventory and out-of-stocks as well as increased revenue and customer satisfaction.
SageQuest,
Solon, OH;
www.sage-quest.com
Year founded: 2003;
Number of employees: 99;
Number of food customers: NA
Solution names: Mobile Control
Markets served: Manufacturers; supermarket retailers; grocery wholesalers; convenience store distributors; foodservice distributors; third-party logistics providers.
Key problems solved: Vehicle tracking, routing and reporting.
SAP America, (a unit of SAP AG),
Newtown Square, PA;
www.sap.com
Year founded: 1972;
Number of employees: 51,400;
Number of food customers: <300
Solution names: ERP 2005; SAP SCM; SAP CRM
Markets served: Manufacturers; supermarket retailers; grocery wholesalers; convenience store distributors; foodservice distributors; third-party logistics providers.
Key problems solved: Corporate financials; purchasing; sales order processing; earned income; returns; inventory planning and management; warehousing; transportation.
ServiceCraft Logistics,
Buena Park, CA;
www.servicecraft.com
Year founded: 1958;
Number of employees: 500;
Number of food customers: 30
Solution names: WMS; TMS; Extranet; Wireless
Markets served: Manufacturers; third-party logistics providers.
Key problems solved: Total supply chain warehousing and distribution support.
*Other solutions/services: Extranet visibility.
ShipXpress,
Jacksonville Beach, FL;
www.shipxpress.com
Year founded: 2000;
Number of employees: 65;
Number of food customers: NA
Solution names: ShipXTRAX; ShipXRATES
Markets served: Manufacturers
Key problems solved: Rail logistics; shipment tracking; rating; freight estimation; rail car lease auditing; various rail accounting functions.
Silvon Software Inc.,
Westmont, IL;
www.silvon.com
Year founded: 1987;
Number of employees: 45;
Number of food customers: 250
Solution names: Stratum
Markets served: Manufacturers; grocery wholesalers; convenience store distributors; foodservice distributors.
Key problems solved: The Stratum suite of planning and performance management applications is designed to leverage vast amounts of information and provide enterprise-wide visibility to our customers by addressing the key operational areas of manufacturing and distribution within their organizations. Stratum helps companies better manage their customer relationships through sales reporting, analysis, and planning that leverages POS, third-party, orders, shipment and A/R data. It allows them to see how well their product categories are performing for their retailers, too, through in-depth category analyses.
*Other solutions/services: Demand forecasting and supply chain performance analysis.
SmartTurn Inc.,
Oakland, CA;
www.smartturn.com
Year founded: 2004
Number of employees: 35;
Number of food customers: 10
Solution names: SmartTurn Inventory and Warehouse Management System; SmartTurn Inventory Grid
Markets served: Manufacturers; grocery wholesalers; foodservice distributors; third-party logistics providers.
Key problems solved: Maintains real-time inventory of food, beverages and supplies to prevent stockouts, overstocks, missing or misplaced items or expired ingredients; improves staff productivity and supplier management by eliminating duplicate data entry errors that cause redundancy; streamlines inventory management, storage and preservation across kitchens and pantries.
Software Logistechs Inc.,
Toledo, OH;
www.softlog.us
Year founded: 1998;
Number of employees: 7;
Number of food customers: 10
Solution names: DC Xpress WMS
Markets served: Manufacturers; supermarket retailers; grocery wholesalers; convenience store distributors; foodservice distributors; third-party logistics providers.
Key problems solved: Management of perishable inventory; improved inventory accuracy to 99%+; elimination of physical inventories; improved labor/operational efficiencies.
SPS Commerce,
Minneapolis;
www.spscommerce.com
Year founded: 1998;
Number of employees: 270;
Number of food customers: 5,000+
Solution names: SPSCommerce.net
Markets served: Manufacturers; supermarket retailers; grocery wholesalers; foodservice distributors; third-party logistics providers.
Key problems solved: More effectively reconcile orders with payments; receive orders and shipments more quickly and accurately; improve the ability to allocate warehouse space and manage inventory; reduce logistics spending; improve supply chain visibility with up-to-date information.
*Other solutions/services: Trading partner intelligence; community development/vendor enablement.
SSI Schaefer Systems International Inc.,
Giebelstadt, Germany;
www.ssi-schaefer-noell.de
Year founded: 1937;
Number of employees: 7,500;
Number of food customers: 37
Solution names: Schaefer Case Picking System (SCP); Schaefer Carousel System (SCS)
Markets served: Manufacturers; supermarket retailers; grocery wholesalers; convenience store distributors; foodservice distributors; third-party logistics providers.
Key problems solved: SSI Schaefer solves space, accuracy, labor and throughput (SALT) issues common in distribution centers of companies experiencing high growth.
Sterling Commerce,
Columbus, OH;
www.sterlingcommerce.com
Year founded: 1974;
Number of employees: 2,675;
Number of food customers: 1,244
Solution names: Sterling Selling and Fulfillment Suite; Connect:Direct; Gentran Integration Suite; Sterling Collaboration Network
Markets served: Manufacturers; foodservice distributors; third-party logistics providers.
Key problems solved: Sterling Commerce offers supply chain solutions, community management and process integration solutions that enable companies to collaborate, share logistics information and therefore better manage the logistics process flow.
*Other solutions/services: Community management; B2B connectivity; supply chain visibility.
Summary Systems,
Plano, TX;
www.summarysystems.com
Year founded: 1987;
Number of employees: 8;
Number of food customers: 3
Solution names: Foodservice Distribution System; Dispatch Commander
Markets served: Manufacturers; foodservice distributors.
Key problems solved: Closing the loop in the distribution chain; enabling 100 percent accurate deliveries; recording delivery exceptions in real-time; reducing short unloads or short-on-truck events; provides proof data to reduce fraudulent claims; reduction in paperwork; pre- and post-trip vehicle inspections; electronic DOT logs.
Supply Chain Consultants,
Wilmington, DE;
www.supplychain.com
Year founded: 1993;
Number of employees: 45;
Number of food customers: 6
Solution names: Zemeter software suite including: Demand Planner; Supply Planner; Inventory Planner; Finite Scheduling; Performance Management; Business Analyst; Zemeter S&OP; Zemeter S&OP Azimuth.
Markets served: Manufacturers.
Key problems solved: Supply Chain Consultants provides collaborative, best-of-breed, fully integrated supply chain solutions that can help manufacturers realize substantial bottom-line results.
*Other solutions/services: Supply chain planning.
Supply Chain Intelligence,
Cary, NC;
www.scintelligence.com
Year founded: 2001;
Number of employees: NA;
Number of food customers: 12
Solution names: iSuite; Outbound Shipment Intelligence; Inbound Shipment Intelligence.
Markets served: Supermarket retailers; grocery wholesalers; convenience store distributors; foodservice distributors.
Key problems solved: Routing and scheduling planning and plan execution for managed fleets. Integrated order splitting and targeted time requirements are used heavily by food industry participants.
Swisslog Logistics Inc.,
Newport News, VA;
www.swisslog.com
Year founded: 1998;
Number of employees: 100;
Number of food customers: 7
Solution names: AS/RS--pallet and case conveyors
Markets served: Manufacturers; supermarket retailers; grocery wholesalers; convenience store distributors.
Key problems solved: Our solutions optimize customers' production, logistics and distribution processes in order to increase flexibility, responsiveness and quality of service while minimizing logistics costs.
Technology Group International,
Toledo, OH;
www.tgiltd.com
Year founded: 1990;
Number of employees: NA;
Number of food customers: NA
Solution names: Enterprise 21
Markets served: Manufacturers; grocery wholesalers; convenience store distributors; foodservice distributors; third-party logistics providers.
Key problems solved: Enterprise 21 includes a wide range of functionality that is needed to support the food industry.
Teradata Corp.,
Dayton, OH;
www.teradata.com
Year founded: 1979;
Number of employees: 5,500;
Number of food customers: 100
Solution names: Enterprise Data Warehouse: Teradata Database 12.0; Customer Management: Teradata Relationship Manager; Demand Chain Management: Teradata Demand Chain Management; Supply Chain Management: Teradata SeeChain; Teradata Supply Chain Accelerator, for SAP; Platform: Teradata
Markets served: Manufacturers; supermarket retailers; grocery wholesalers; convenience store distributors; foodservice distributors; third-party logistics providers.
Key problems solved: Better predicting product assortments that will drive the most profitable customers to purchase; reducing out-of-stocks, overstocks and slow moving inventory to improve margins.
Terra Technology,
Norwalk, CT;
www.terratechnology.com
Year founded: 2001;
Number of employees: 35;
Number of food customers: 15
Solution names: Demand Sensing; Inventory Optimization; Multi-Enterprise Demand Sensing; Multi-Enterprise Inventory Optimization
Markets served: Manufacturers
Key problems solved: Inaccurate forecasts result in manufacturing and shipping the wrong product mix. Manufacturers produce excess inventory to avoid losing sales, wasting resources producing and shipping products with unexpectedly low demand and incurring the cost of unplanned manufacturing changeovers and expedited shipments to meet demand for high demand products. Terra's solutions apply better math to the planning process; improving service while reducing manufacturing disruptions, expedited shipments and safety stock requirements.
TGW-Ermanco Inc.,
Spring Lake, MI;
www.tgw-ermanco.com
Year founded: 1964;
Number of employees: 240;
Number of food customers: 100+
Solution names: Integrated material handling solutions
Markets served: Manufacturers; supermarket retailers; grocery wholesalers; convenience store distributors.
Key problems solved: Labor savings; improved space utilization; reduced order-fulfillment time.
*Other solutions/services: Integrated material handling solutions.
TLC--Total Logistic Control,
Holland, MI;
www.totallogistic.com
Year founded: 1902;
Number of employees: 2,400;
Number of food customers: 165
Solution names: Transportation management and warehouse management solutions
Markets served: Manufacturers; supermarket retailers; grocery wholesalers; convenience store distributors; foodservice distributors; third-party logistics providers
Key problems solved: TLC supply chain capabilities are "source to shelf." We operate across the key supply chain functions and bring the supporting technology. TLC targets companies which are interested in outsourcing all or portions of supply chain operations and/or supply chain technologies.
Tom Zosel Associates Ltd. (TZA),
Chicago;
www.tzaconsulting.com
Year founded: 1984;
Number of employees: 44;
Number of food customers: 51
Solution names: ProTrack Warehouse Labor Management System; Protrack Driver; ProTrack Mobile; Slot3D
Markets served: Manufacturers; supermarket retailers; grocery wholesalers; convenience store distributors; foodservice distributors; third-party logistics providers
Key problems solved: Best practices, engineered standards and SOPs implemented to improve labor management, productivity and lower costs.
*Other solutions/services: Slot3D slotting technology.
ToolsGroup,
Boston;
www.toolsgroup.com
Year founded: 1993;
Number of employees: 65;
Number of food customers: 21
Solution names: Service Optimizer 99+
Markets served: Manufacturers; supermarket retailers; grocery wholesalers; convenience store distributors; foodservice distributors; third-party logistics providers.
Key problems solved: Inventory optimization; supply chain performance management; demand sensing and demand management
Transervice Logistics Inc.,
Lake Success, NY;
www.transervice.com
Year founded: 1969;
Number of employees: 1,350;
Number of food customers: 13
Solution names: Dedicated transportation and maintenance solutions; dedicated contract carriage; full-service leasing; maintenance
Markets served: Manufacturers; supermarket retailers; grocery wholesalers; convenience store distributors; foodservice distributors; third-party logistics providers.
Key problems solved: Implementing seamless transitions from private fleets to dedicated contract fleets without disruption.
*Other solutions/services: Dedicated transportation and maintenance solutions.
Transplace,
Frisco, TX;
www.transplace.com
Year founded: 2000;
Number of employees: 526;
Number of food customers: 100+
Solution names: Transplace Transportation Management System; Transplace Order Management System; Scenario Pro Shipment Planning; Trailer Management
Markets served: Manufacturers; supermarket retailers; grocery wholesalers; convenience store distributors; foodservice distributors.
Key problems solved: Inbound /outbound shipment planning and optimization; improved operational efficiency while reducing cost; accurate and timely payment process to improve cash flow; route and mode analysis reducing network costs; determined appropriate placement for distribution centers; faster, on-time pickup and delivery; diversified LTL carriers mix for improved service.
TranSystems,
Kansas City, MO;
www.transystems.com
Year founded: 1966;
Number of employees: 1,400;
Number of food customers: 75
Solution names: Network Design and Optimization; Strategic Global Consulting; Carbon Footprint Analysis; Transportation and Real Estate Analysis; LEED and Environmental Services; Architecture/Engineering; Simulation Modeling; Construction Management; Material Handling and Facility Design; Demand Planning and Forecasting; Supply Chain Technology and Security; Systems Integration and Implementation
Markets served: Manufacturers; supermarket retailers; grocery wholesalers; foodservice distributors; third-party logistics providers.
Key problems solved: Improved process flows; designed effective plant operations; reduced labor costs; implemented and integrated supply chain technologies and systems.
UPS Logistics Technologies,
Baltimore;
www.upslogisticstech.com
Year founded: 1983;
Number of employees: 150;
Number of food customers: 675
Solution names: Roadnet Transportation Suite which includes: Territory Planner, Roadnet and MobileCast. Roadnet Anywhere for smaller fleets that want planning and tracking technology.
Markets served: Manufacturers; supermarket retailers; grocery wholesalers; convenience store distributors; foodservice distributors; third-party logistics providers.
Key problems solved: Driver accountability for hours, miles driven, unplanned stops and other route exceptions; reduce miles driven, overtime and vehicle wear and tear; accurate real-time vehicle location; vehicle utilization.
Virtual Dispatch USA Inc.,
Grand Haven, MI;
www.virtualdispatch.com
Year founded: 1996;
Number of employees: 10;
Number of food customers: 20+
Solution names: Excelerate.
Markets served: Manufacturers; foodservice distributors; third-party logistics providers.
Key problems solved: Carrier management; fuel surcharge; advanced communication; supply chain visibility; load planning; EDI; ACE compliance.
Voxware Inc.,
Hamilton, NJ;
www.voxware.com
Year founded: 1996;
Number of employees: 90;
Number of food customers: 25
Solution names: VoiceLogistics; Voxware 3
Markets served: Manufacturers; supermarket retailers; grocery wholesalers; convenience store distributors; foodservice distributors; third-party logistics providers.
Key problems solved: Increase warehouse workforce productivity; decrease order picking errors; improve warehouse workforce safety; maximize IT investments; optimize current material handling processes; obtain the best ROI possible for any warehouse automation project.
*Other solutions/services: Voice-based warehouse distribution.
Weber Distribution,
Santa Fe Springs, CA;
www.weberdistribution.com
Year founded: 1924;
Number of employees: 540;
Number of food customers: 96
Solution names: LINKS by Synapse Warehouse Management System; Translinks Transportation Management System
Markets served: Manufacturers; supermarket retailers; grocery wholesalers; convenience store distributors; foodservice distributors; third-party logistics providers.
Key problems solved: High velocity distribution; seasonal peaks; VAS; integrated warehouse and transportation.
*Other solutions/services: Retail compliance; refrigerated warehouse and transportation.
Werner Enterprises Inc.,
Omaha;
www.werner.com
Year founded: 1956;
Number of employees: 13,000;
Number of food customers: 150+
Solution names: Smart (Shipment Management and Resource Tracking) System
Markets served: Manufacturers; supermarket retailers; grocery wholesalers; convenience store distributors; foodservice distributors; third-party logistics providers.
Key problems solved: Collaborate efforts between multiple shippers which continues to reduce costs in the industry between Warner and its customers.
*Other solutions/services: Optimization/continuous moves.
West Monroe Partners,
Chicago;
www.westmonroepartners.com
Year founded: 2002;
Number of employees: 250;
Number of food customers: 10
Solution names: Engineered Labor Standards (Services); FLEXdls (Labor Management System)
Markets served: Manufacturers; supermarket retailers; grocery wholesalers; convenience store distributors; foodservice distributors; third-party logistics providers.
Key problems solved: We help develop programs that enable distribution centers and retailers to achieve and maintain their peak efficiency. Specifically, our programs will evaluate and measure labor activities and create standards that will help our clients to plan, track and improve daily operations. We also help our clients deploy the standards through comprehensive training and incentive programs that ensure success.
*Other solutions/services: Labor management.
Westfalia Technologies Inc.,
York, PA;
www.westfaliausa.com or www.savanna.com
Year founded: 1992;
Number of employees: 90;
Number of food customers: 60+
Solution names: Savanna.NET Warehouse Management System
Markets served: Manufacturers; third-party logistics providers.
Key problems solved: Savanna.NET warehouse management system helps develop an efficient warehousing system, which in turn increases profitability, reduces inventory costs and distributes products to clients faster. With its flexible modular structure, the WMS can be configured on individual logistics requirements, integrated into new or existing structures and is ideal for both conventional and automated facilities.
*Other solutions/services: Automated equipment integration.
Witron Integrated Logistics Corp.,
Arlington Heights, IL;
www.witron.com
Year founded: 1971;
Number of employees: 1,200;
Number of food customers: 30
Solution names: OPM-Order Picking Machinery; DPS-Dynamic Picking System; OPS-Order Picking System; MPS-Module Picking System; CPS-Car Picking System; E-DPS-Ergonomic Dynamic Picking System
Markets served: Manufacturers; supermarket retailers; grocery wholesalers; convenience store distributors; foodservice distributors.
Key problems solved: Automated picking efficiencies; labor reduction; inventory reduction; material flow synchronization.
XATA Corp.,
Minneapolis;
www.xata.com
Year founded: 1985;
Number of employees: 167;
Number of food customers: 105+
Solution names: XATANet; MobileMax
Markets served: Manufacturers; supermarket retailers; grocery wholesalers; convenience store distributors; foodservice distributors; third-party logistics providers.
Key problems solved: Cost issues: fleet MPG; driving styles; idling time control; driver performance; delay tracking; operational efficiency. Regulatory compliance issues: fuel tax; paperless driver logs; safety and inspections; "black box" functions. Customer service issues: managing delivery windows; real-time truck location; instant notifications of time deviations.
Zebra Technologies,
Vernon Hills, IL;
www.zebra.com
Year founded: 1969;
Number of employees: 2,400;
Number of food customers: NA
Solution names: Zebra Technologies is a leading global provider of rugged and reliable specialty printing solutions, including on-demand thermal bar code label and receipt printers and supplies, plastic card printers, RFID smart label printer/encoders, certified smart media, and digital photo printers
Markets served: Manufacturers; supermarket retailers; grocery wholesalers; convenience store distributors; foodservice distributors; third-party logistics providers.
Key problems solved: Inventory control; mobile technology; RFID; routing and scheduling; security; supply chain management; transportation management; warehouse management; wireless technology; yard management.