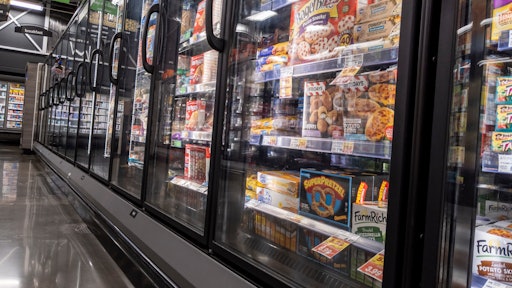
The frozen food category is heating up in the United States, with strong growth over recent years. Emerging trends toward healthy lifestyles, coupled with waste-conscious consumers seeking affordability and convenience, are expected to drive the value of cold chain logistics by $647.47 billion by 2028.
However, amidst this promising outlook lies a crucial challenge—maintaining such high volumes of frozen food products at proper temperatures. Approximately 13% of all food produced globally is lost annually due to inadequate cold storage.
Advancements in technology will play a critical role in tackling this problem and shaping the future of the frozen food industry. Recent strides to integrate technology that optimizes storage and transportation logistics are empowering suppliers to preserve the quality and timely delivery of frozen food. Learn more about how these innovations such as leveraging digital twins, computer vision, and machine learning are overcoming key industry challenges.
Optimizing logistics with digital twins
Digital twin technology offers significant potential to optimize frozen food logistics by providing a virtual representation of physical assets and processes. This technology is particularly transformative in planning logistics and ensuring seamless deliveries.
An innovative solution for enhancing storage and transportation logistics is the implementation of a digital twin to create a 3D digital replica of the entire warehouse. Within a cold storage facility, different areas are designated for specific purposes, such as refrigerated units, blast-freezing zones, and intermediate spaces. Digital twins continuously monitor temperatures and conditions of storage facilities, refrigerated trucks, and shipping containers in real time. By integrating sensors alongside digital twins, suppliers can ensure frozen food is stored within the required temperature range throughout the entire supply chain, minimizing the risk of spoilage.
Additionally, goods can spoil during transportation or due to delays in warehouse processes. For instance, some large facilities span 2 million square feet with over 10,000 locations. In these setups, where there are a huge number of shipments being transported, it is crucial to avoid slow-moving freight causing congestion. Technology such as digital twins could be pivotal to avoiding congestion and delays—mitigating risks of food spoilage, wasted energy and waste.
Leveraging computer vision to mitigate spoilage risks
Issues such as packaging integrity, mishandling, contamination, spoilage (resulting from improper inventory management), and temperature abuse (such as storing food at room temperature instead of the required zero degrees) can lead to physical damage in supply chains. These problems contribute significantly to the staggering 1.4 billion pounds of food wasted annually.
Computer vision systems play a crucial role in addressing these challenges. By analyzing images of products as they move through distribution centers, these systems can detect signs of physical damage, including those caused by temperature variations.
Armed with this information, organizations can take proactive measures to mitigate further damage to their products and optimize their supply chain operations. For instance, staff can manually inspect the affected products to assess the extent of the damage and determine whether they are safe for consumption or need to be discarded.
Alternatively, the distribution center can promptly address the malfunctioning refrigeration unit or adjust the temperature settings, preventing further temperature variations and minimizing the risk of damage to other products stored in the same area.
Cutting energy costs with machine learning
CBS News found reports energy prices are rocketing—energy consumption is one of the largest expenses for manufacturers and suppliers and costs can be even more significant for frozen food producers and suppliers. According to Make UK, 60% of bosses are increasingly concerned about energy blackouts affecting business, and 64% stated higher energy costs are among the biggest risks to their company. Some manufacturers around the world have even reported that their energy bills have tripled, according to the Business Times.
Machine learning (ML) algorithms are able to analyze historical data, external weather conditions, and the thermal properties of frozen goods to optimize temperature control systems in storage facilities and transportation vehicles. By dynamically adjusting temperature setpoints based on real-time conditions and predictive models, ML algorithms can minimize energy consumption while ensuring that frozen goods remain within the required temperature range.
ML algorithms also have the potential to predict future patterns and trends, an added advantage for companies looking to bolster their sustainability endeavors and stay on top of energy consumption and costs.
Conclusion
Technology innovations such as digital twins, computer vision and machine learning all serve to power factory and supply chain efficiency for businesses in the frozen food industry.
Adopting these innovative tools will help manufacturers and suppliers address the biggest sector concerns such as energy consumption, food waste and spoilage, and delivery delays while keeping high costs at bay.
Additionally, these technologies will empower suppliers to keep pace with high consumer demand for frozen food, without compromising on quality of delivery.